Financial Accounting
FinAcct ERP Provides End to End solutions in Financial Accounting inncluding General Ledger transactions, Invoices, Payments, Agewise Analysis, Profit & Loss account, Balance Sheet and Cash Flow.
Cash / Bank
Transact Receipts, Payments, Withdrawals, Deposits, Contra and Reconcile bank statement.
Journal
Add Journal vouchers for provisional transactions and TDS Journal exclusively to make TDS provisions.
Reports
- General Transactions
- Ledger Transactions
- Bank Transactions
- Output and Input Payments
- Trial Balance
- Profit and Loss Account
- Balance Sheet
- Cash Flow
- Agewise Analysis
- Cost Centre Analysis
- Variance Analysis
Import
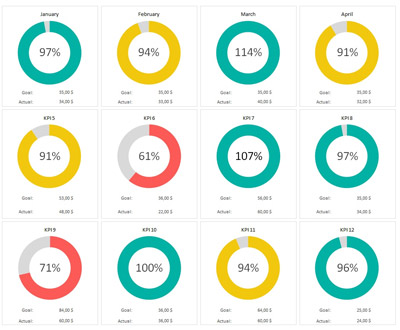
- Bank Transactions
- Cash Transactions
- Invoice Transactions
- Ledger Group
- Ledger
- Tally Master
- Tally Voucher
- Customer Master
- Vendor Master
- Employee Master
- Salary
- Stock Item
- Inventory Transactions
- Physical Stock at Location
- GRN Import
- Stock Delivery Import
Budget
Manage budgets for expenses accounts and actual with variance analysis report.
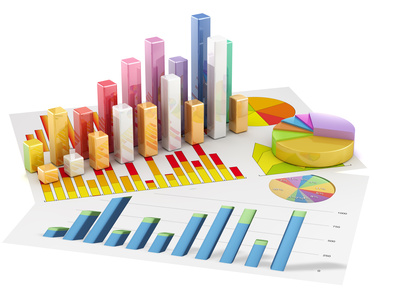
- Region wise budget
- Branch wise budget
- Department wise budget
- Group wise
- Ledger wise
- Profit Centre budget
- Variance Analysis Report Quarter wise
ERP Supply Chain Management - Sales
Manage sales through quotation by updating information and proceed to Sales order, Sales delivery , Sales invoice by click of few button.
Quotations
Send quotation to clients through e-mails and confirm to proceed or cancel.
Orders
Add Customer Name, Ref. No. , Date, Item description, Quantity and Price and proceed to sales order or against sales quotation.
Deliveries
Deliver stocks through outstanding sales order OR directly generate sales delivery.
Invoicing
Raise sales invoice against delivery with GST compliant for B2B and B2C customers and generate E-Way Bill for applicable invoices also raise sales invoice against Job Order and Work Order.
Collections
Receive amount from clients by Cash or Bank and adjust against amount receivable.
ERP Supply Chain Management - Purchases
Manage Purchases through order by updating information and proceed to GRN, Purchase Invoice by click of few buttons.
Quotations
Send quotation to clients through e-mails and confirm to proceed or cancel.
Orders
Add Supplier Name, date, Ref. No., Supplier Invoice No., Item Description, Quantity and Price and proceed to Purchase Order.
GRN
Receives stock against Outstanding PO or directly generate GRN.
Purchase Invoices
Raise Purchase Invoice against GRN.
Returns
Records stock returns against invoices by suppliers against reference.
Reports
- Outstanding PO
- Completed PO
- GRN
- Invoice
- Debit Notes
ERP Supply Chain Management - Inventory
Comprehensive Inventory management features for small and mid size companies.
Products
Manage products with ID, Code and detailed attributes like Product type, Category, Sub Category, Brand, Class, and Sub class etc.
Batches
Batch number can be allotted or items Purchased to track Location, Qty In, Qty Out, Qty In Hand based on Date range and location.
Multiple Units
Maintain products in base and alternate measurement units also convert from one unit to another.
Locations
Maintain inventory across multiple locations with details 0f status tock in hand, stock transfer etc.
Re-Order
Manage, maintain stocks to reorder with minimum and maximum levels. View reorder reports of stocks to be ordered.
Warehouse Management
Manage, maintain stocks in warehouse in a location determined by Rack, Bin. It also manages stock movement from one warehouse, rack, bin to another warehouse, rack and bin
Reports
- Stock Item
- Stock Movement Analysis
- Stock Summary
- Stock Quantity On Hand (QOH)
- Stock Inward
- Stock Outward
- Warehouse Movement analysis
Production & Manufacturing
Manufacturing
Manage manufacturing process by choosing a series of transactions or through a single transaction.
Bill of Material
Create and manage finished goods, semi finished goods with multilevel Bill Of Materials. You can also add component with additional details to complete the process.
Production Routing
Add and configure stages in the production process as routing of given finished good.
Work Order
Create work order from confirmed Sales order. User can specify the required quantity and release date of the final goods.
Work Order Issue
Issue Raw materials for a given Work Order from locations required for manufactured goods internally with date of requirement.
MRP
It helps user to check the input raw material demand for given finished goods in all the work order.
MPS
It shows the overall schedule in work week for all the finished goods.
Production Enquiry and Design
The requirement of finished good from prospects is captured in enquiry for given number and due date. The overall production design is speculated in design record with planned resource, machines and labour as per given design document.
Design BOM and Final BOM
It helps the user to design multi level semi finished goods with length, thickness, width, given quantity and raw material input. Design BOM once confirmed is converted to final BOM mentioned earlier. This module helps semi-finished good BOM to be also created from raw material input
Design Process and Routing
It allows the user to add and configure production process stages with or without semi finished good. The user needs to convert these process stages into final routing master
Production Planning & Control
Production record is created from each Work order with tentative start and end date. For each Production schedule, it creates as many Job Tasks as there are routing stages. Each Job task is scheduled and tracked with given labour and machine
Finished Good Inspection
After finished good is produced, quality inspection is recorded and inspection result is measured.
Job Order
Customer order can be taken in the form of Job Order of IN type. Production Control record is created from Job Order and finished good produced like from that of Work Order
Receivables and Payables
Receivables and Payables
Receivables
It shows all the sales and service invoices from all the customers. User can manage all receivables by accepting payment from customers and transactions are recorded in Financial Accounting Module.
Payables
It shows all the purchase and input service invoices from all the suppliers. User can manage all payables and dues by making payment to suppliers and transactions are recorded in Financial Accounting Module.